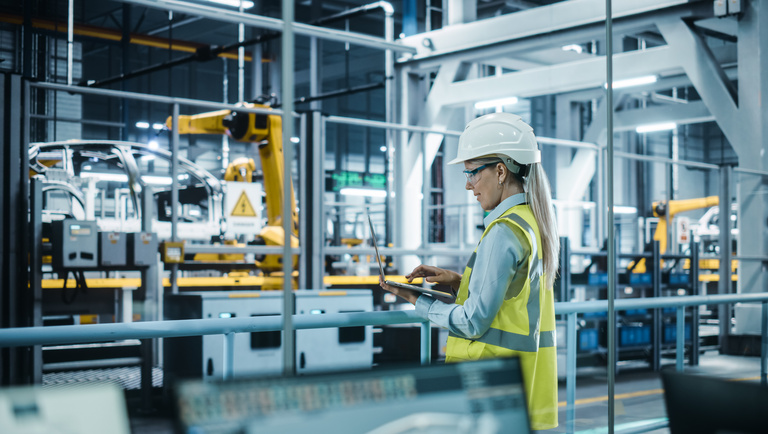
- Blog , Engineering & Production
- Published on: 12.03.2025
- 11:05 mins
Modularization: The Key to Greater Efficiency in E/E Development
The electronics and electrical development (E/E development) sector is under immense pressure: increasing product complexity, a growing share of software components, and the need to bring innovations to market faster and more cost-effectively pose major challenges for companies. At the same time, demand for cutting-edge electronic solutions is rapidly rising in industries such as automotive, mechanical engineering, and medical technology. How can companies handle these challenges while maintaining control over quality, budget, and timelines?
The answer lies in a strategic approach: modularization. Modularization forms the foundation for standardization and automation – two key factors that make development processes more efficient and conducive to innovation. Supported by Model-Based Systems Engineering (MBSE) and Model-Based Design (MBD), both products and processes can be sustainably optimized while creating a competitive advantage.
In this article, we explore how modularization serves as the backbone of productive electronics development and how MBSE and MBD help meet the challenges of modern product complexity.
The Challenges of Today's E/E Development
E/E development is at the heart of many forward-looking industries, from automotive and medical technology to mechanical engineering. It brings together disciplines such as hardware, software, and systems integration to create innovative solutions with a wide range of applications.
Despite its critical role, E/E development faces numerous challenges that significantly impact an organization’s competitiveness and productivity. To ensure long-term success, companies must overcome the following hurdles:
- Managing complexity: Today’s products and development processes are becoming increasingly complex. Coordinating mechanics, electronics, and software requires systematic approaches to efficiently manage dependencies and ensure smooth operations.
- Handling product variability efficiently: The growing number of product variants often leads to organizational and technical bottlenecks. Without structured variant management, resources are used inefficiently, and processes stall.
- Ensuring short lead times: Time is a critical competitive factor. Delays in development can have a significant impact on market success. Companies need solutions that help them get products from concept to market readiness faster.
- Guaranteeing consistent quality: Maintaining high product quality is difficult without standardization. Faulty or insufficiently tested components not only jeopardize customer satisfaction but also drive up costs due to returns and rework.
- Increasing reusability: Many companies miss the opportunity to effectively reuse existing components. Instead, modules and solutions are repeatedly developed from scratch, wasting time and resources.
- Optimizing costs and efficiency: Lack of automation and inefficient processes drive up costs. In highly competitive industries, this waste of resources is unsustainable in the long term.
- Avoiding resource overload: Skilled professionals often spend too much time on routine tasks, limiting capacity for strategically important and innovative work. The result: diminished innovation potential and increased team frustration.
The goal is to achieve high cost-efficiency in established products through standardization and automation. This approach helps to conserve company resources, allowing them to be redirected toward exploring innovative market opportunities. The following chart illustrates how companies can strategically align efficiency with added customer value.
The visualization highlights how established products focus on efficiency, while innovative solutions prioritize high customer value. Model-based approaches such as MBSE, MBD, and MES enable companies to bridge these two dimensions. By combining standardization and automation, established products can be optimized for cost-effectiveness while freeing up resources for the development of groundbreaking solutions.
MBSE, MBD, and MES as Solution Approaches
To meet the challenges of balancing efficiency and customer value, companies are turning to modular approaches and configure-to-order strategies. Combined with systems engineering methods such as MBSE, MBD, and MES, they can not only increase productivity but also reduce time-to-market and create room for innovation.
What is MBSE (Model-Based Systems Engineering)?
Model-Based Systems Engineering (MBSE) is a systematic approach that uses models, rather than documents, as the central working foundation. These models are used to efficiently and transparently manage requirements, specifications, system architectures, and functional analysis.
A key advantage of MBSE is its holistic view of complex systems. By using digital models, all relevant domains, such as electrical, electronic, mechanical, and software can be integrated and combined into a consistent product architecture. This enables early identification and resolution of interface issues and promotes better communication between different disciplines.
What is MBD (Model-Based Design)?
Model-Based Design (MBD) focuses on creating standardizable and reusable modules within a system. MBD uses digital models to design, simulate, and optimize individual components or assemblies.
With MBD, you benefit from using simulation-capable models that allow you to validate design decisions early – without the need to create physical prototypes. This allows you to identify and address potential problems in the conceptual phase, reducing development time and costs. Additionally, by standardizing, you increase the reuse of already tested and quality-assured modules. This increases the efficiency and effectiveness of the development process and reduces time-to-market.
What is a MES (Manufacturing Execution System)?
A Manufacturing Execution System (MES) is a software-based solution that monitors, controls, and optimizes operational manufacturing processes in real time. Using a model-based approach, the MES automatically receives manufacturing information from the configure-to-order process, which is based on a standardized module catalog. Production-relevant is prepared to be consistent, complete, and accurately aligned with the product requirements.
An MES offers many benefits. Firstly, it increases production efficiency by utilizing high-quality, well-coordinated, and often reusable building blocks, which reduces error rates and ensures consistent manufacturing quality. Secondly, it frees up valuable engineering capacity by automating routine tasks in the production process, allowing engineers to focus on strategically important and innovative projects. This optimized allocation of resources not only boosts a company's competitiveness but also fosters the development of new products and technologies.
How MBSE and MBD Integration Works
The integration of MBSE, MBD, and MES enables a seamless connection between concept, development, and production. This model-based approach ensures that requirements, modules, and production processes are efficiently aligned. The following graphic illustrates how these approaches work together in a continuous development process.
- As shown in the diagram, the process starts with the architecture phase within MBSE. Here, requirements are systematically grouped and represented in system models that serve as the central basis for the product architecture and the E/E architecture. These models integrate all relevant requirements, define the framework for implementation, and facilitate the management of complex systems. MBSE thus provides a structured and efficient foundation for development.
- In the realization phase, MBD is used to translate the results of the architecture phase into simulation-capable components, modules, and products. Using MBD leverages standardized and tested modules, allowing for early evaluation of design decisions and ensuring maximum reuse of proven building blocks.
- Finally, in the production phase, an MES ensures that the standardized modules and models from MBSE and MBD are efficiently used in manufacturing. Automated processes, based on the configure-to-order principle, ensure smooth, efficient, and error-free production steps. This seamless integration of all phases results in more efficient E/E development, shorter time-to-market, and higher product quality.
The three key elements of model-based development
Model-based development relies on three fundamental elements: models, modules, and products. These components form the foundation for an efficient and structured development process, enabling reusability and standardization. The following graphic illustrates how these elements interact within E/E development and contribute to the success of the development process.
The process begins with the creation of digital models that represent the requirements, specifications, and analyses of a product or its individual components. From these models, standardized modules are developed that are designed to be both reusable and compatible. Finally, by combining models and modules, finished products are created that can be flexibly adapted to customer requirements.
Modularization as an Optimization for Standardization
The combination of MBSE, MBD, and MES provides a strong foundation for E/E development: While MBSE handles architectural planning, MBD takes care of operational implementation, and MES links development to production. At the heart of this approach is modularization – a strategic method that sustainably optimizes both processes and products.
Modularization is far more than just a tool for increasing efficiency. It allows for a greater number of identical components within standard modules, unlocking purchasing potential. At the same time, modular approaches enable functional improvements and provide targeted solutions for challenges in production and transportation. To fully realize these benefits, however, it is essential to carefully analyze and integrate the company's vision and mission into the optimization process.
When applied strategically, modularization makes standardization a reality – offering a critical competitive advantage in today’s product development environment. Reusable modules and the refinement of proven components free up valuable resources that can be invested in true innovation. Artificial intelligence can significantly accelerate this process: AI-driven analyses identify optimal modules for standardization and reuse, driving data-driven optimization.
However, reuse should never be an end in itself. A modular approach only makes sense if the benefits – such as cost efficiency and time savings – outweigh the drawbacks of customized adaptations. Solutions based on standard modules must always be more economical and faster than bespoke developments.
Evaluate and optimize your strategy regularly
Successful implementation requires a cross-departmental perspective and a comprehensive PMTO assessment (analyzing processes, tools, methods, and organization). This approach helps achieve a balanced integration of configure-to-order (CTO) and engineer-to-order (ETO), enabling efficient fulfillment of standardized and customer-specific requirements.
Professional Expertise for Reliable Results
When it comes to implementation, MHP provides comprehensive support in adapting your processes and systems for the seamless integration of MBSE and MBD. Leverage our expertise in modular and automated processes to optimize your E/E development. Our services include:
- Methodology and Process Consulting: Through an independent analysis of existing electronic processes, we identify areas for improvement and advise on the optimal integration of MBSE and MBD approaches into your company’s structure.
- Integration into PLM environments: We ensure the seamless incorporation of model-based methods into existing PLM systems, managing the transition from document-based to model-based processes while ensuring consistent implementation.
- Requirements analysis: MHP identifies and defines the requirements for modularization and automation processes, including the creation of detailed specifications for PTMO components.
- Modularization and automation: Our experts develop strategies for introducing or extending modular product platforms for hardware and software development. We also help maximize reusability through modular architectures.
- Implementation of advanced technologies: We create customized roadmaps for the strategic integration of advanced automation and standardization tools. In addition, we provide comprehensive support for the implementation and customization of PLM, ALM, and authoring systems that effectively enhance MBSE and MBD. We also assist you in building a scalable infrastructure that enables simulation-based and model-driven development.
Leverage the Benefits of Model-Based Systems Engineering Methods
While manufacturing challenges are vast and complex, model-based approaches such as MBSE and MBD provide essential solutions for managing the increasing complexity of modern products. By seamlessly linking requirements, architectures, and disciplines, they establish a strong foundation for high quality and shorter development cycles. At the same time, reusable modules and automated processes open up new opportunities to increase efficiency and achieve sustainable cost reductions.
For your company, this means:
- Faster time-to-market: Accelerate product launches and gain a critical competitive advantage.
- Higher product quality: Improve profitability, customer satisfaction, and long-term business success through consistent, high-quality outcomes.
- Focus on innovation: Automation reduces routine tasks, freeing resources for strategically important and innovative projects.
To help you unlock the full potential of modularization, standardization, and automation, MHP offers a holistic approach – from precise requirements analysis to successful implementation. As an experienced partner in electronics development and IT consulting, we accompany you every step of the way.
Starting with a personalized potential analysis, you receive concrete recommendations tailored to your industry and specific needs. Our experienced experts support you in implementing these measures, helping you build an E/E development process that is not only efficient and profitable but also future-proof.
FAQs
With MBSE and MBD, complex systems can be managed through a structured, model-based analysis of requirements, functions, and modules. MBSE lays the foundation for standardization and discipline integration, while MBD translates this approach into simulation-capable, reusable modules and components for electronics development. Together, they ensure more efficient processes, higher quality, and shorter development times.
Modularization reduces product complexity by breaking systems down into manageable, standardized building blocks that are flexibly reusable. These modules can be applied in various configurations without the need for extensive adjustments.
MHP assists companies through a neutral analysis of existing processes. This analysis forms the foundation for developing targeted measures for realignment or optimization, enabling the integration of MBSE and MBD approaches into existing structures.
The duration of integrating MBSE and MBD depends on the complexity of existing processes and systems, as well as the maturity of the organization. Typically, the process can take anywhere from a few months to a year, including analysis, concept development, and implementation. Initial optimization potentials, based on existing company capabilities and technologies, can often be identified and quantified within a few months.
By implementing MBSE and MBD, your company can realize significant savings potential. Total development costs can be reduced by up to 55%, while on-time project completions increase by 23%. Additionally, you can shorten time-to-market by 20 to 30%, reduce rework due to communication issues by 50%, and improve product quality by approximately 62%.